Optimizing Inventory Process using Physics Informed ML
Improving asset efficiency, through research in inventory management across various MSME segments The project is particularly suited for manufacturing MSMEs with multi-stage production processes, such as foundries, machining units, textiles, food processing, and FMCG sectors. These segments often grapple with balancing raw material procurement, work-in-progress bottlenecks, and finished goods demand volatility. The model’s compartmental structure aligns with their production lifecycle, enabling precise tracking and optimization of inventory across stages. For instance, foundries managing metal casting (raw → molten metal → finished parts) or food processors handling perishable ingredients benefit from AI- driven demand forecasting and cost-minimization. These industries face high risks of stockouts, overstocking, or resource wastage, making the framework’s real-time adjustments and holistic cost optimization critical for enhancing operational efficiency and resilience.
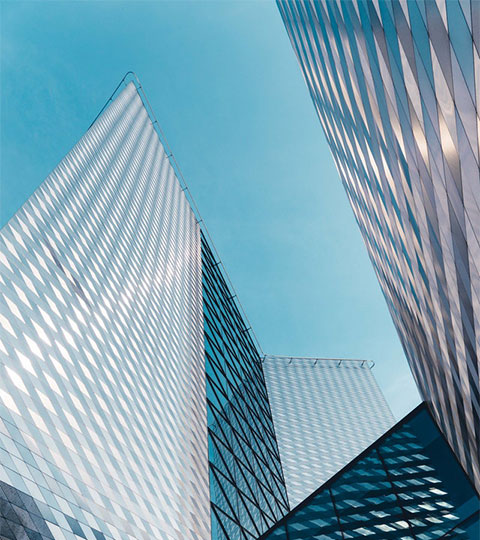
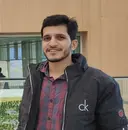
Key Features of the Project
AI Pontryagin Optimization: Combines Pontryagin’s Maximum Principle with neural networks for dynamic, system-wide inventory control across raw materials, work-in progress, and finished goods.
Holistic Compartmental Modeling: Simultaneously tracks all inventory stages using epidemiology-inspired models, avoiding siloed decision-making.
Real-Time Supply Chain Synchronization: Coordinates production, inventory, and delivery plans globally with alerts for stockouts, overstocking, or disruptions.
LSTM Demand Forecasting: Predicts demand trends via Long Short-Term Memory networks to optimize